ERAIL ELECTRIFIED RAIL SYSTEMS*
Electrified Rail Systems are a complete power supply suspension system that can be used in combination with a Knight Servo System, VFD tractors, power tools, and other electrical devices.
The ERAD Series is a fully enclosed electrical system that eliminates the stack-up of runway festooning. The power travels through a conductor power rail (ERail), mounted on top of Knight’s ERAD4000, ERAD6000, or ERAD7000 ergonomically friendly aluminum rail. The standard ERail is equipped with (4) four poles, nominal current 60 amp, 240/480V which can run multiple systems on (1) one rail assembly.
The Electrified Rail is incredibly diverse in that it can also be mounted to the side of the aluminum rail. The benefits to this configuration include shorter stack-up heights and the use of Knight’s standard rail rather than the custom rail used with the top-mounted style. The side-mounted style can also be retrofitted onto an existing Knight system to eliminate the need for electrical festooning.
*Top-mounted style is Patent Pending
General Information
+Features
- Patent Pending
- Fully Enclosed Electrical System
- ERail Electrical Capacity:
Up to 60 amps / 690 volts - Horizontal curved sections available.
- Max Weight Capacity:
Up to 3,000 lbs [1,360 kg] - Compliant with International Standards.
- Added safety against shock.
- Knight’s unique hanger design allows for adjustments while leveling the system.
Benefits
- Optional mounting configuration: side mounted.
- Eliminates stack-up of festooning trolleys and hanging electrical cables.
- Simplifies installation by including electrical rail within suspension.
- Eliminates need for tow bars.
- Stacked compact design eliminates need from installing load rail and power rail separately.
- Twice the power of the competition.
System Components
+
ERail
Available in 4 poles with a nominal current of 60 A.
ERail Conductor Trolley
Travels inside of the ERail and is combined with the Knight load trolley. Copper graphite shoes are used for energy and control voltages over 35 V.
ERAD4000/ERAD6000/ERAD7000
Combined with Knight’s load trolleys, provides the most ergonomically friendly rail system. Rail comes in lengths up to 25ft [9.1m] without a splice. Capacities up to 3,000 lbs. [1,360 kg].
Suspension Points
Knight adjustable hangers and End Trucks support both the Load Rail and ERail. Hangers have the ability to mount to I-Beams, C-Channels, Angle Iron, and many others.
ERail End Caps and Stops
Attaches to the end of the ERail Series Rail. The Redundant End Cap is primarily used to prevent load and ERail trolleys from exiting the rail.
Power Supply End Feed
Power supply feed for ERail. Comes standard with 4 poles.
ERAD4000 Capacity Chart
+ERAD4000 Capacities
Hanger Span | Deflection Criteria | ||||||
---|---|---|---|---|---|---|---|
1:350 Capacity* | 1:450 Capacity* | 1:550 Capacity* | |||||
ft | m | lbs | kg | lbs | kg | lbs | kg |
5 | 1.52 | 1140 | 517 | 1140 | 517 | 1140 | 517 |
6 | 1.83 | 945 | 429 | 945 | 429 | 945 | 429 |
7 | 2.13 | 810 | 367 | 810 | 367 | 790 | 358 |
8 | 2.45 | 705 | 320 | 705 | 320 | 600 | 272 |
9 | 2.74 | 625 | 283 | 575 | 261 | 470 | 213 |
10 | 3.05 | 560 | 254 | 460 | 209 | 375 | 170 |
11 | 3.35 | 490 | 222 | 375 | 170 | 300 | 136 |
12 | 3.66 | 405 | 184 | 310 | 141 | 245 | 111 |
13 | 3.96 | 340 | 154 | 255 | 116 | 205 | 93 |
14 | 4.27 | 285 | 129 | 215 | 98 | 170 | 77 |
15 | 4.57 | 240 | 109 | 180 | 82 | 140 | 64 |
16 | 4.88 | 205 | 93 | 150 | 68 | 120 | 54 |
17 | 5.18 | 175 | 79 | 130 | 59 | 100 | 45 |
18 | 5.49 | 150 | 68 | 110 | 50 | 80 | 36 |
19 | 5.79 | 130 | 59 | 90 | 41 | 65 | 29 |
20 | 6.10 | 110 | 50 | 75 | 34 | 55 | 25 |
21 | 6.40 | 90 | 41 | 60 | 27 | 40 | 18 |
22 | 6.71 | 80 | 36 | 50 | 23 | 30 | 14 |
23 | 7.01 | 65 | 29 | 40 | 18 | 20 | 9 |
24 | 7.32 | 50 | 23 | 30 | 14 | 15 | 7 |
*Due to Ergonomic considerations, each rail span distance is tested to determine the maximum single point load required to achieve a predetermined deflection based on a ratio of 1:350 (1” of deflection for each 350” of length), 1:450 (1” of deflection in 450” of length) or 1:550 (1” of deflection for each 550” of length).
For purposes of estimating approximate ergonomic force requirements, the following formula may be used:
0.009 x total mass = maximum effort (in lbf) required to overcome inertia. Effort required to sustain movement is generally 0.35 x effort to overcome inertia e.g.,
250 lbs. (1.03 kg) mass x 0.009 = 2.25 lbf (0.9 kg) to overcome inertia
2.25 (0.9 kg) x 0.35 = .79 lbf (0.36 kg) to sustain movement
ERAD6000 Capacity Chart
+ERAD6000 Capacities
Hanger Span | Deflection Criteria | ||||||
---|---|---|---|---|---|---|---|
1:350 Capacity* | 1:450 Capacity* | 1:550 Capacity* | |||||
ft | m | lbs | kg | lbs | kg | lbs | kg |
5 | 1.52 | 2030 | 921 | 2030 | 921 | 2030 | 921 |
6 | 1.83 | 1690 | 767 | 1690 | 767 | 1690 | 767 |
7 | 2.13 | 1445 | 655 | 1445 | 655 | 1445 | 655 |
8 | 2.45 | 1260 | 572 | 1260 | 572 | 1260 | 572 |
9 | 2.74 | 1115 | 506 | 1115 | 506 | 1115 | 506 |
10 | 3.05 | 1000 | 454 | 1000 | 454 | 895 | 406 |
11 | 3.35 | 905 | 411 | 900 | 408 | 730 | 331 |
12 | 3.66 | 825 | 374 | 750 | 340 | 605 | 274 |
13 | 3.96 | 760 | 345 | 630 | 286 | 510 | 231 |
14 | 4.27 | 700 | 318 | 535 | 243 | 430 | 195 |
15 | 4.57 | 600 | 272 | 455 | 206 | 365 | 166 |
16 | 4.88 | 520 | 236 | 395 | 134 | 310 | 141 |
17 | 5.18 | 450 | 204 | 340 | 154 | 270 | 122 |
18 | 5.49 | 395 | 179 | 295 | 134 | 230 | 104 |
19 | 5.79 | 345 | 156 | 255 | 116 | 195 | 88 |
20 | 6.10 | 300 | 136 | 220 | 100 | 170 | 77 |
21 | 6.40 | 265 | 120 | 190 | 86 | 145 | 66 |
22 | 6.71 | 230 | 104 | 165 | 75 | 125 | 57 |
23 | 7.01 | 205 | 93 | 140 | 64 | 105 | 48 |
24 | 7.32 | 180 | 82 | 120 | 54 | 85 | 39 |
*Due to Ergonomic considerations, each rail span distance is tested to determine the maximum single point load required to achieve a predetermined deflection based on a ratio of 1:350 (1” of deflection for each 350” of length), 1:450 (1” of deflection in 450” of length) or 1:550 (1” of deflection for each 550” of length).
For purposes of estimating approximate ergonomic force requirements, the following formula may be used:
0.009 x total mass = maximum effort (in lbf) required to overcome inertia. Effort required to sustain movement is generally 0.35 x effort to overcome inertia e.g.,
250 lbs. (1.03 kg) mass x 0.009 = 2.25 lbf (0.9 kg) to overcome inertia
2.25 (0.9 kg) x 0.35 = .79 lbf (0.36 kg) to sustain movement
ERAD7000 Capacity Chart
+ERAD7000 Capacities
Hanger Span | Deflection Criteria | ||||||
---|---|---|---|---|---|---|---|
1:350 Capacity* | 1:450 Capacity* | 1:550 Capacity* | |||||
ft | m | lbs | kg | lbs | kg | lbs | kg |
5 | 1.52 | 3000 | 1360 | 3000 | 1360 | 3000 | 1360 |
6 | 1.83 | 3000 | 1360 | 3000 | 1360 | 3000 | 1360 |
7 | 2.13 | 3000 | 1360 | 3000 | 1360 | 3000 | 1360 |
8 | 2.45 | 2940 | 1334 | 2940 | 1334 | 2940 | 1334 |
9 | 2.74 | 2610 | 1184 | 2610 | 1184 | 2610 | 1184 |
10 | 3.05 | 2345 | 1064 | 2345 | 1064 | 2345 | 1064 |
11 | 3.35 | 2130 | 966 | 2130 | 966 | 2130 | 966 |
12 | 3.66 | 1945 | 882 | 1945 | 882 | 1945 | 882 |
13 | 3.96 | 1795 | 814 | 1795 | 814 | 1720 | 780 |
14 | 4.27 | 1660 | 753 | 1660 | 753 | 1475 | 669 |
15 | 4.57 | 1545 | 701 | 1545 | 701 | 1275 | 578 |
16 | 4.88 | 1445 | 655 | 1370 | 621 | 1110 | 503 |
17 | 5.18 | 1355 | 615 | 1205 | 547 | 975 | 442 |
18 | 5.49 | 1280 | 581 | 1065 | 483 | 860 | 390 |
19 | 5.79 | 1205 | 547 | 950 | 431 | 765 | 347 |
20 | 6.10 | 1105 | 501 | 845 | 383 | 680 | 308 |
21 | 6.40 | 995 | 451 | 760 | 345 | 610 | 277 |
22 | 6.71 | 895 | 406 | 685 | 311 | 545 | 247 |
23 | 7.01 | 810 | 367 | 615 | 279 | 490 | 222 |
24 | 7.32 | 735 | 333 | 555 | 252 | 440 | 200 |
*Due to Ergonomic considerations, each rail span distance is tested to determine the maximum single point load required to achieve a predetermined deflection based on a ratio of 1:350 (1” of deflection for each 350” of length), 1:450 (1” of deflection in 450” of length) or 1:550 (1” of deflection for each 550” of length).
For purposes of estimating approximate ergonomic force requirements, the following formula may be used:
0.009 x total mass = maximum effort (in lbf) required to overcome inertia. Effort required to sustain movement is generally 0.35 x effort to overcome inertia e.g.,
250 lbs. (1.03 kg) mass x 0.009 = 2.25 lbf (0.9 kg) to overcome inertia
2.25 (0.9 kg) x 0.35 = .79 lbf (0.36 kg) to sustain movement
Videos
+*ERail Electrified Rail Systems
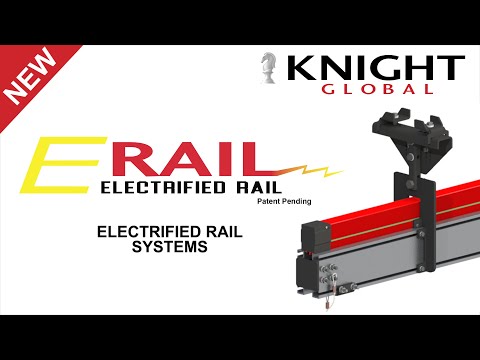
Accessories
General
+Filter by Rail Type
- Secures electrical cord for the power.
- Used in conjunction with the ERail trolley to prevent damage to the cable.
- Travels inside of the ERail.
- Carries power to the electrical tools on the ERail System.
- Copper graphite shoes are used for energy and control voltages over 35 V.
- 240VAC, single phase or 480VAC, 3 phase power.
- Includes the EMRMA6172 Cord Clamp.
- 15AMP, 20AMP, or 30AMP
- Includes 1 meter or 3 meter electrical cable.
- Used to clean the inside of the electrified rail.
- Equipped with a nylon brush trolley for cleaning.
Hangers
+Filter by Rail Type
- Suspends Knight’s ERAD4000 series rail and Knight’s ERail.
- For Direct or Offset loads.
- Attaches to all C-Channel or Angle Iron.
- Adjustable Hanger Height.
- Structural steel can be run perpendicular or parallel to the rail system.
- Suspends Knight’s ERAD4000 series rail and Knight’s ERail.
- For Direct or Offset loads.
- Steel can be run parallel or perpendicular to the rail system.
- Suspends Knight’s ERAD4000, ERAD6000, or ERAD7000 Series Rail.
- For Direct or Offset Loads.
- Fixed Height Hanger.
- Hanger is clamped to the top flange of the Knight rail.
- Coated with an environmentally friendly corrosion protection. ** (Autophoretic ACC 900®).
- Attaches to all C-Channel or Angle Iron.
- Suspends Knight’s ERAD6000 series rail and Knight’s ERail.
- For Direct or Offset loads
- Steel can be run parallel or perpendicular to the rail system.
- Adjustable Hanger Height.
- Suspends Knight’s ERAD6000 series rail and Knight’s ERail.
- For Direct or Offset loads
- Steel can be run parallel or perpendicular to the rail system.
- Adjustable Hanger Height.
- Suspends Knight’s ERAD7000 series rail and Knight’s ERail.
- For Direct or Offset loads
- Steel can be run parallel or perpendicular to the rail system.
- Adjustable Hanger Height.
- Suspends Knight’s ERAD7000 series rail and Knight’s ERail.
- For Direct or Offset loads
- Steel can be run parallel or perpendicular to the rail system.
- Adjustable Hanger Height.
- Suspends Knight’s ERAD4000 series rail and Knight’s ERail.
- For Direct or Offset loads
- Steel can be run parallel or perpendicular to the rail system.
- Structural Support Flange Size: 2 in. – 7 in. [51mm – 178mm].
- Adjustable Hanger Height.
- Suspends Knight’s ERAD4000 series rail and Knight’s ERail.
- For Direct or Offset loads
- Steel can be run parallel or perpendicular to the rail system.
- Structural Support Flange Size: 7 in. – 11 in. [178mm – 279mm].
- Adjustable Hanger Height.
- Suspends Knight’s ERAD6000 series rail and Knight’s ERail.
- For Direct or Offset loads
- Steel can be run parallel or perpendicular to the rail system.
- Structural Support Flange Size: 2 in. – 7 in. [51mm – 178mm].
- Adjustable Hanger Height.
- For Direct Loads.
- Structural Support Flange Size: 2 in.- 7 in. [51mm – 178mm].
- Used for the non-electrified side of an ERail system.
- Coated with an environmentally friendly corrosion protection. ** (Autophoretic ACC 900®).
- Adjustable Height Hanger.
- Suspends Knight’s ERAD6000 series rail and Knight’s ERail.
- For Direct or Offset loads
- Steel can be run parallel or perpendicular to the rail system.
- Structural Support Flange Size: 7 in. – 11 in. [178mm – 279mm].
- Adjustable Hanger Height.
- Suspends Knight’s ERAD7000 series rail and Knight’s ERail.
- For Direct or Offset loads.
- Steel can be run parallel or perpendicular to the rail system.
- Structural Support Flange Size: 2 in. – 7 in. [51mm – 178mm].
- Adjustable Hanger Height.
- Suspends Knight’s ERAD7000 series rail and Knight’s ERail.
- For Direct or Offset loads
- Steel can be run parallel or perpendicular to the rail system.
- Structural Support Flange Size: 7 in. – 11 in. [178mm – 279mm].
- Adjustable Hanger Height.
Load Trolleys
+Filter by Rail Type
- Travels inside of the ERail.
- Carries power to the electrical tools on the ERail System.
- Copper graphite shoes are used for energy and control voltages over 35 V.
- 240VAC, single phase or 480VAC, 3 phase power.
- Includes the EMRMA6172 Cord Clamp.
- 15AMP, 20AMP, or 30AMP
- Includes 1 meter or 3 meter electrical cable.
- Attaches to a Knight Servo Hoist and runs inside of the ERAD4000 Series rail system.
- Fiberglass filled High Impact Nylon Wheels.
- Side Guide Rollers with integrated bearings.
- Double-shielded bearings keep dirt out and do not require lubrication.
- Suspends a load from Knight’s ERAD4000 Series rail system.
- Fiberglass filled High Impact Nylon Wheels.
- Side Guide Rollers with integrated bearings.
- Double-shielded bearings keep dirt out and do not require lubrication.
- Suspends a load from Knight’s ERAD4000 Series rail system.
- Fiberglass filled High Impact Nylon Wheels.
- Side Guide Rollers with integrated bearings.
- Double-shielded bearings keep dirt out and do not require lubrication
- Suspends a load from Knight’s ERAD4000 Series rail system.
- Fiberglass filled High Impact Nylon Wheels.
- Side Guide Rollers with integrated bearings.
- Double-shielded bearings keep dirt out and do not require lubrication.
- Suspends a load from Knight’s ERAD4000 Series rail system.
- Fiberglass filled High Impact Nylon Wheels.
- Side Guide Rollers with integrated bearings.
- Double-shielded bearings keep dirt out and do not require lubrication.
- Attaches to a Knight Servo Hoist and runs inside of the ERAD6000 Series rail system.
- Fiberglass filled High Impact Nylon Wheels.
- Side Guide Rollers with integrated bearings.
- Double-shielded bearings keep dirt out and do not require lubrication.
- Suspends a load from Knight’s ERAD6000 Series rail system.
- Fiberglass filled High Impact Nylon Wheels.
- Side Guide Rollers with integrated bearings.
- Double-shielded bearings keep dirt out and do not require lubrication.
- Suspends a load from Knight’s ERAD6000 Series rail system.
- Fiberglass filled High Impact Nylon Wheels.
- Side Guide Rollers with integrated bearings.
- Double-shielded bearings keep dirt out and do not require lubrication.
- Suspends a load from Knight’s ERAD6000 Series rail system.
- Fiberglass filled High Impact Nylon Wheels.
- Side Guide Rollers with integrated bearings.
- Double-shielded bearings keep dirt out and do not require lubrication.
- Suspends a load from Knight’s ERAD6000 Series rail system.
- Fiberglass filled High Impact Nylon Wheels.
- Side Guide Rollers with integrated bearings.
- Double-shielded bearings keep dirt out and do not require lubrication.
- Attaches to a Knight Servo Hoist and runs inside of the ERAD7000 Series rail system.
- Fiberglass filled High Impact Nylon Wheels.
- Side Guide Rollers with integrated bearings.
- Double-shielded bearings keep dirt out and do not require lubrication.
- Suspends a load from Knight’s ERAD7000 Series rail system.
- Fiberglass filled High Impact Nylon Wheels.
- Side Guide Rollers with integrated bearings.
- Double-shielded bearings keep dirt out and do not require lubrication.
- Suspends a load from Knight’s ERAD7000 Series rail system.
- Fiberglass filled High Impact Nylon Wheels.
- Side Guide Rollers with integrated bearings.
- Double-shielded bearings keep dirt out and do not require lubrication.
- Suspends a load from Knight’s ERAD7000 Series rail system.
- Fiberglass filled High Impact Nylon Wheels.
- Side Guide Rollers with integrated bearings.
- Double-shielded bearings keep dirt out and do not require lubrication.
- Suspends a load from Knight’s ERAD7000 Series rail system.
- Fiberglass filled High Impact Nylon Wheels.
- Side Guide Rollers with integrated bearings.
- Double-shielded bearings keep dirt out and do not require lubrication.
- Used to clean the inside of the electrified rail.
- Equipped with a nylon brush trolley for cleaning.
End Trucks
+Filter by Rail Type
- Suspends Knight’s ERAD4000 Series Rail and ERail.
- The EMRES4181-4000 runs inside of the RAD4110 Series Rail.
- Yoke design allows for pivoting in the “X” and “Y” directions.
- Suspends Knight’s ERAD4000 Series Rail and the ERail.
- EMRES4185-4000 runs inside of Knight’s RAD4110 Series Rail.
- Yoke design allows for pivoting in the “X” and “Y” directions.
- Suspends Knight’s ERAD6000 Series Rail and ERail.
- Yoke design allows for pivoting in the “X” and “Y” directions.
- The EMRES6181-4000 runs inside of the RAD4110 Series Rail.
- The EMRES6181-6000 runs inside of the RAD6110 Series Rail.
- The EMRES6181-7000 runs inside of the RAD7510 Series Rail.
- Suspends Knight’s ERAD6000 Series Rail and the ERail.
- Yoke design allows for pivoting in the “X” and “Y” directions.
- EMRES6185-4000 runs inside of Knight’s RAD4110 Series Rail.
- EMRES6185-6000 runs inside of Knight’s RAD6110 Series Rail.
- EMRES6185-7000 runs inside of Knight’s RAD7510 Series Rail.
- Suspends Knight’s ERAD7000 Series Rail and ERail.
- Yoke design allows for pivoting in the “X” and “Y” directions.
- The EMRES7181-4000 runs inside of the RAD4110 Series Rail.
- The EMRES7181-6000 runs inside of the RAD6110 Series Rail.
- The EMRES7181-7000 runs inside of the RAD7510 Series Rail.
- Suspends Knight’s ERAD7000 Series Rail and the ERail.
- Yoke design allows for pivoting in the “X” and “Y” directions.
- EMRES7185-4000 runs inside of Knight’s RAD4110 Series Rail.
- EMRES7185-6000 runs inside of Knight’s RAD6110 Series Rail.
- EMRES7185-7000 runs inside of Knight’s RAD7510 Series Rail.
End Caps / Stops
+Filter by Rail Type
- Attaches to the end of the ERAD4000 Rail and ERail.
- Primarily used to prevent a load trolley from exiting the rail.
- Attaches to the end of the ERAD4000 Rail and ERail.
- Primarily used to prevent a load trolley from exiting the rail.
- Attaches to the end of Knight’s ERail.
- Prevents dust from getting inside of the rail.
- Attaches to the end of the ERAD6000 Rail and ERail.
- Primarily used to prevent a load trolley from exiting the rail.
- Attaches to the end of the ERAD6000 Rail and ERail.
- Primarily used to prevent a load trolley from exiting the rail.
- Attaches to the end of the ERAD7000 Rail and ERail.
- Primarily used to prevent a load trolley from exiting the rail.
- Attaches to the end of the ERAD7000 Rail and ERail.
- Primarily used to prevent a load trolley from exiting the rail.
- Attaches to the end of Knight’s ERAD4000 Series Rail and ERail.
- Prevents a load trolley or end truck from exiting the rail.
- Attaches to the end of the ERAD4000 Series Rail and ERail.
- Primarily used to prevent a load trolley from exiting the rail.
- Attaches to the end of Knight’s ERAD6000 Series Rail and ERail.
- Prevents a load trolley or end truck from exiting the rail.
- Attaches to the end of the ERAD6000 Series Rail and ERail.
- Primarily used to prevent a load trolley from exiting the rail.
- Attaches to the end of Knight’s ERail and ERAD7000 Series Rail.
- Primarily used to prevent an End Truck or Load Trolley from exiting the rail.
- Attaches to the end of Knight’s ERail and the ERAD7000 Series Rail.
- Primarily used to prevent a load trolley or end truck from exiting the rail.
Splice Kits
+Filter by Rail Type
- Used to splice together (2) sections of ERail and (2) sections of ERAD4000 or ERAD6000 series rail.
- Bolt-on splice kit.
- Provides easier access to bolt heads.
- Eliminates the need to weld bosses.
- Bolt on splice kit for ERail and ERAD7000 Series Rail.
- Provides easier access to bolt heads.
- Eliminates need to weld bosses.